Understanding Metal Lathe Machine Parts: A Comprehensive Guide
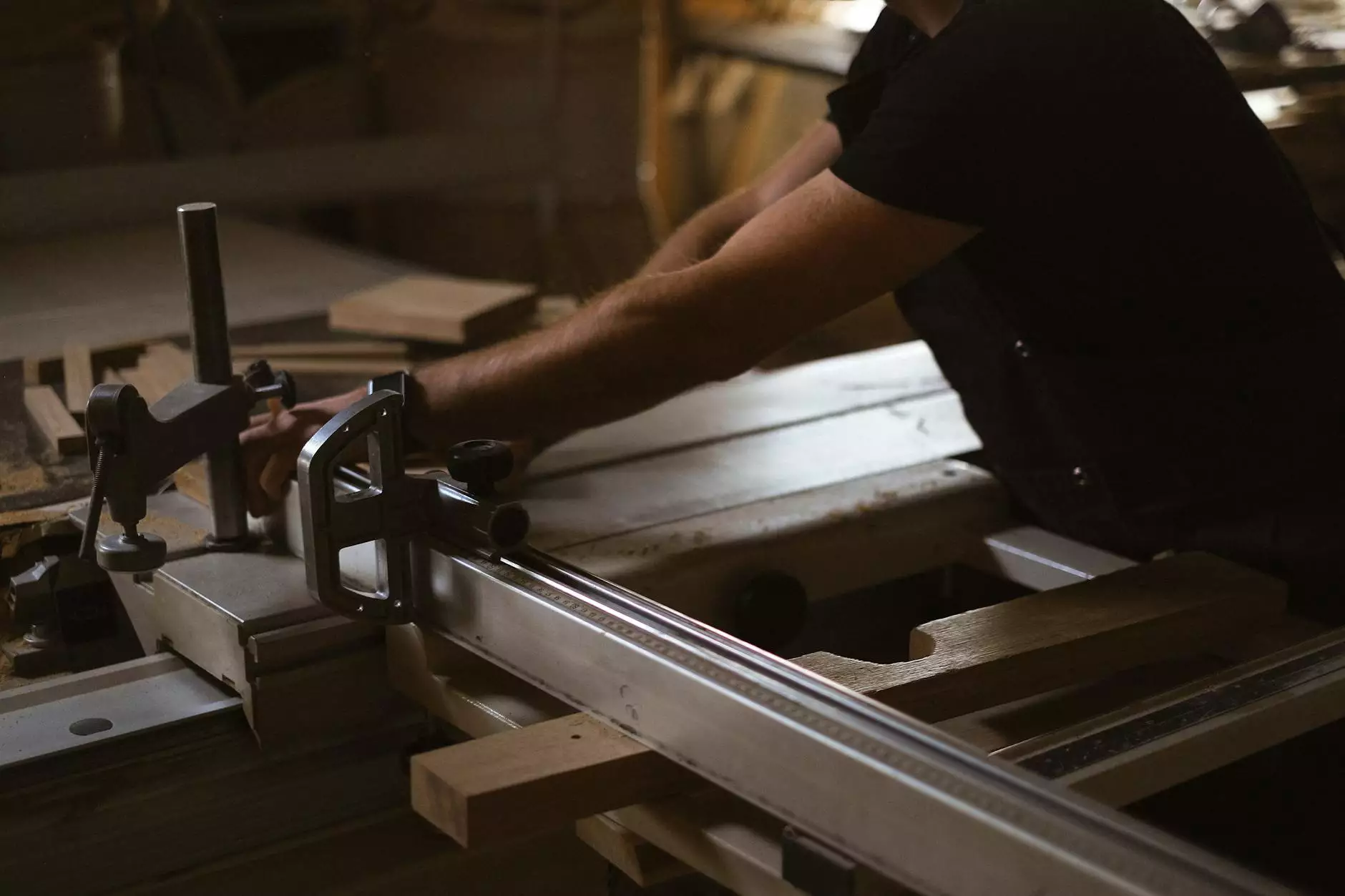
The Importance of Metal Lathe Machines in Modern Manufacturing
In the realm of metal fabrication, metal lathe machines stand out as essential tools. They are pivotal for shaping, cutting, and finishing metal components. A metal lathe machine can turn raw materials into precise parts used across various industries, including automotive, aerospace, and manufacturing. Understanding the components that make up these machines is crucial for ensuring optimal performance and longevity.
Key Components of Metal Lathe Machines
A metal lathe comprises several components, each serving a unique function. Knowledge of these parts not only enhances operational efficiency but also aids in maintenance and troubleshooting. Here, we delve into the essential metal lathe machine parts:
- Headstock: The headstock houses the main motor and the drive mechanism. It provides power to the spindle, enabling rotation.
- Tailstock: This component is adjustable and can be moved along the bed. It supports longer workpieces and houses tools like drill bits.
- Bed: The bed is the foundation of the lathe. It must be rigid and precise, providing stability to the machine and ensuring accurate machining.
- Carriage: The carriage moves the cutting tool(s) along the bed, accommodating different machining tasks.
- Cross Slide: This part adjusts the tool's position vertically, allowing for more complex cuts.
- Tool Post: The tool post secures the cutting tool in place during operation, ensuring accurate cut depths and angles.
- Spindle: This is the part that holds and rotates the workpiece while it is being machined. Its speed can be adjusted for various tasks.
- Chuck: The chuck grips the workpiece tightly, stabilizing it through the machining process. Various types exist to accommodate different shapes and sizes of stock.
- Apron: Located at the front of the carriage, the apron houses the controls for moving the carriage.
- Feed Mechanism: This controls how the cutting tool moves relative to the workpiece, affecting the finish and accuracy of the cut.
Exploring Each Component in Detail
1. Headstock
The headstock is arguably the most critical part of the lathe. It houses various mechanisms and can have multiple speeds, allowing for versatility during operations. High-quality headstocks contribute to the machine's ability to perform fine cuts, vastly improving overall product quality.
2. Tailstock
The tailstock offers stability for longer pieces and enables the operation of various tools like drill bits and taps. Its ability to slide along the bed ensures adaptability for different workpiece lengths.
3. Bed
The bed's stability is fundamental for accurate machining. A poorly constructed bed can lead to vibrations that affect the finish and precision of the cut. Thus, investing in a well-built lathe with a solid bed is crucial for any metal fabrication workshop.
4. Carriage
The carriage uses a combination of gears and levers to adjust the cutting tool's position accurately. It provides the necessary support to ensure that the cut is straight and true.
5. Cross Slide
The cross slide adds versatility, as it allows for vertical adjustments of the cutting tool. This functionality is important when different depths of cut are required.
6. Tool Post
The tool post is responsible for holding the cutting tool securely during operation. A rigid tool post minimizes flex and vibrations, which could affect cutting performance.
7. Spindle
The spindle's precision is vital; a well-balanced and smooth-running spindle will help in achieving high-quality finishes and minimize tool wear.
8. Chuck
The chuck plays an important role by gripping the workpiece firmly. Different types of chucks (three-jaw, four-jaw, or collet) cater to various workpiece shapes and sizes, providing enhanced options for fabricators.
9. Apron
The apron houses controls that allow the operator to maneuver the carriage. Understanding these controls is key to mastering lathe operations.
10. Feed Mechanism
The feed mechanism essentially controls how fast the cutting tool moves across the workpiece. Adjustments to the feed rate can have significant effects on both the speed of machining and the quality of the finish.
Importance of Maintaining Metal Lathe Machine Parts
Regular maintenance of metal lathe machine parts is essential to prolong their lifespan and maintain optimal performance. Here are some maintenance tips:
- Lubrication: Regularly lubricate moving parts to reduce friction and wear.
- Inspection: Routinely inspect components for wear and tear, and replace any parts that show signs of damage.
- Cleaning: Keep the lathe and its parts clean from metal shavings and debris to prevent corrosion and other issues.
- Calibration: Regularly calibrate the machine to ensure that it maintains its precision over time.
- Proper Training: Make sure operators are adequately trained in both the use and maintenance of the lathe.
The Future of Metal Lathe Technology
The field of metal lathe machines is continually evolving. Advanced technologies such as CNC (Computer Numerical Control) lathes are transforming manufacturing processes. These modern machines offer improved precision, flexibility, and reduced human error, heralding a new era for metal fabrication.
As more industries adopt CNC technology, the demand for traditional lathes remains, especially for specific applications where manual intervention is preferred for intricate designs. Future advancements will likely focus on integrating smart technologies, facilitating real-time monitoring and automation, leading to enhanced efficiency in machining operations.
Conclusion
Understanding the various metal lathe machine parts and their functions is essential for anyone involved in metal fabrication. From the headstock to the feed mechanism, each component plays a significant role in delivering high-quality machining results. By maintaining these parts and embracing emerging technologies, businesses at deepmould.net can ensure they stay competitive and produce exceptional metal components for various applications.
For more insights and updates on metal fabrication and machinery, keep visiting deepmould.net.