Understanding GRP Composite Housings: The Future of Sustainable Packaging Solutions
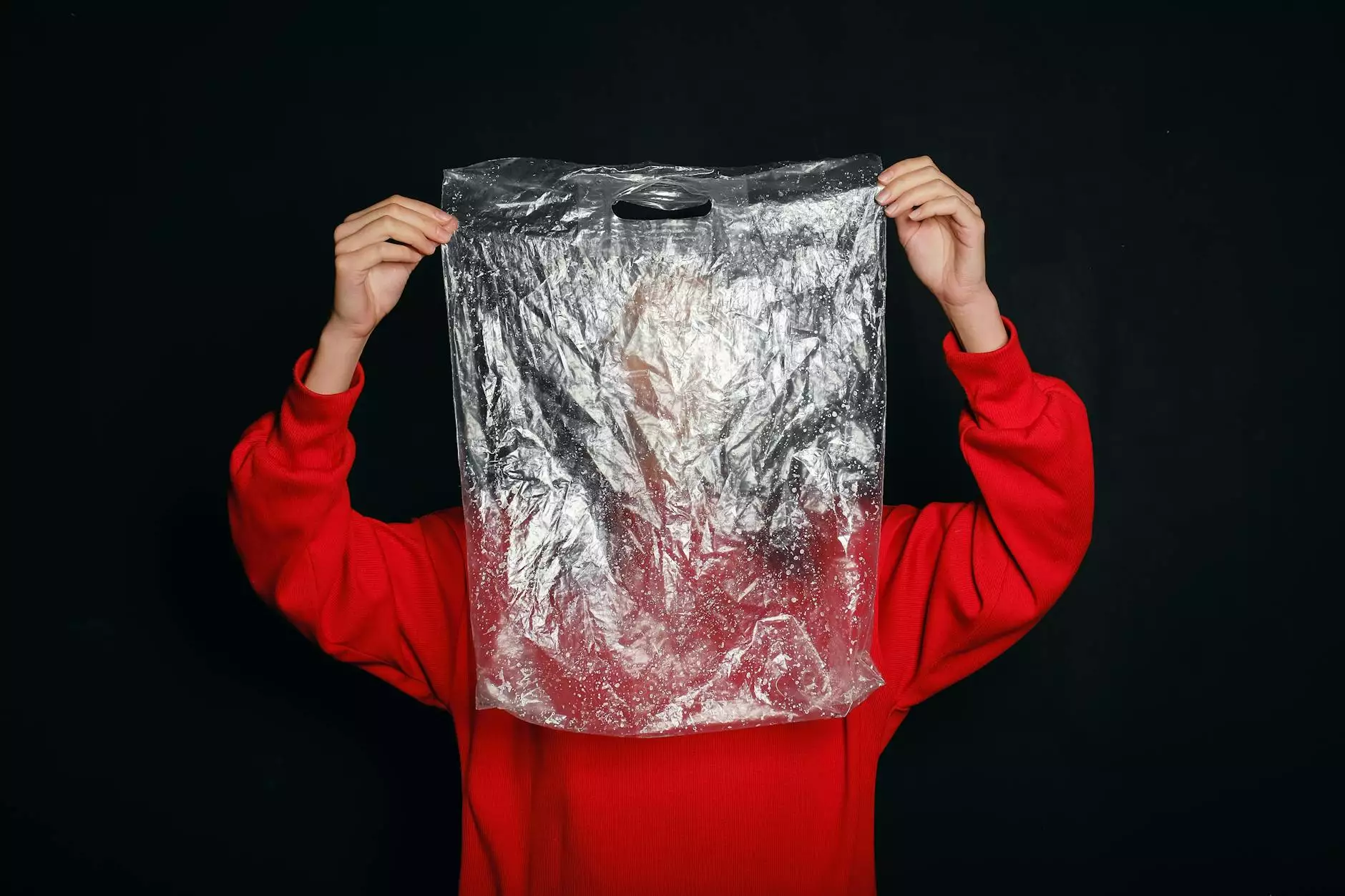
In today's ever-evolving industrial landscape, GRP composite housings have emerged as a vital component in a range of applications, including telecommunications, electrical, and utility sectors. This article delves into the intricacies of Glass Reinforced Plastic (GRP) composite housings, detailing their advantages, applications, manufacturing processes, and the innovative solutions offered by Celtic Composites.
What are GRP Composite Housings?
GRP composite housings are engineered structures made from a blend of glass fibers and plastic resins, forming a composite material that combines the strength of glass with the lightweight properties of plastics. These housings are designed to protect sensitive electronic equipment, ensuring longevity and reliability in harsh environments. The durability, corrosion resistance, and lightweight nature of GRP materials make them an ideal choice over traditional materials.
Key Characteristics of GRP Composite Housings
- Corrosion Resistance: Unlike metal housings, GRP materials do not corrode, making them suitable for outdoor use in various climates.
- Lightweight: Their reduced weight allows for easier handling and installation, particularly in applications requiring elevated or remote placements.
- Customizability: GRP composites can be molded into various shapes and sizes, allowing for tailored solutions that meet specific client needs.
- Thermal Insulation: GRP materials offer excellent thermal insulation, protecting sensitive electronics from extreme temperature fluctuations.
Applications of GRP Composite Housings
The versatility of GRP composite housings allows them to find applications across a multitude of industries. Some noteworthy examples include:
1. Telecommunications
In the telecommunications sector, GRP composite housings are extensively used for housing telecommunication equipment. Their durability ensures that sensitive electronics are shielded from environmental factors such as rain, humidity, and temperature extremes.
2. Electrical Utilities
Utility companies utilize GRP housings to protect electrical components from the elements. The lightweight nature and corrosion resistance extend the lifespan of the equipment, while reducing maintenance costs associated with traditional metal housings.
3. Transportation and Automotive
The automotive industry has embraced GRP composite housings for various applications, from engine covers to battery enclosures. Their ability to withstand harsh conditions and their lightweight properties contribute to enhanced fuel efficiency.
4. Marine Applications
In marine environments, GRP composite housings are favored for their resistance to saltwater corrosion. They protect critical equipment on ships and offshore installations, ensuring operational reliability in challenging conditions.
5. Renewable Energy
With the growing trend of renewable energy solutions, GRP composite housings are increasingly being used in wind turbines and solar panels. Their durability aids in extending the operational life of these systems.
Manufacturing Processes of GRP Composite Housings
The manufacturing of GRP composite housings typically involves several steps to ensure a robust and quality end product:
1. Material Selection
High-quality glass fibers and plastic resins are selected to ensure that the composite material exhibits the desired strength and performance characteristics.
2. Molding Techniques
Commonly used molding techniques include:
- Hand Layup: This manual process involves laying glass fibers in a mold and applying resin by hand, providing excellent control over material placement.
- Spray-Up: In this method, chopped glass fibers and resin are sprayed into the mold, allowing for quicker production but with slightly less control over material orientation.
- RTM (Resin Transfer Molding): This process involves placing dry glass fabric into a mold and injecting resin under pressure, leading to higher quality and consistent results.
3. Curing
The composite material is then cured to harden it, either at room temperature or elevated temperatures in an oven. This step is crucial for achieving the desired strength and durability.
4. Finishing
Finally, the cured housings may undergo finishing processes such as sanding, painting, or the addition of protective coatings to enhance aesthetics and further improve performance.
Advantages of GRP Composite Housings
The rise in popularity of GRP composite housings can be attributed to numerous advantages:
1. Sustainability
As industries shift towards more sustainable practices, GRP composites offer a solution due to their long lifespan and recyclability. Celtic Composites is committed to utilizing eco-friendly materials and processes, contributing to a greener future.
2. Cost-Effectiveness
While initial costs may be higher than traditional metal housing alternatives, the long-term savings associated with reduced maintenance and extended lifespan position GRP composites as a cost-effective solution.
3. Enhanced Safety
GRP materials are non-conductive and minimize the risk of electric shock, an essential safety feature in electrical and telecommunications applications.
Challenges and Considerations
Despite their many benefits, GRP composite housings do face certain challenges:
1. Material Brittleness
While GRP is strong, it can be brittle under certain stress conditions, necessitating careful design consideration to prevent failure.
2. UV Stability
Initial materials can degrade when exposed to UV light over extended periods. However, using UV-stabilized resins can mitigate this issue.
Celtic Composites: Leading the Way in GRP Solutions
Celtic Composites is a pioneering company in the manufacture of GRP composite housings, demonstrating expertise and innovation. With a strong focus on quality and sustainability, they provide customized solutions tailored to meet the specific needs of their clients.
With state-of-the-art facilities and an experienced team, Celtic Composites ensures that all products meet rigorous industry standards. Their commitment to customer satisfaction and continuous improvement places them at the forefront of the composite technology industry.
Conclusion
In conclusion, the future of packaging and protection in various industries is leaning towards GRP composite housings. Their numerous benefits, coupled with the innovative advancements from leaders like Celtic Composites, demonstrate a significant shift towards more environmentally-friendly, durable, and cost-effective solutions. As industries continue to recognize the advantages of these materials, we can anticipate greater adoption and development in the realm of composite technologies.
For further information about GRP composite housings and how Celtic Composites can support your business needs, visit celticcomposites.co.uk.